Our big backyards–our playgrounds, our adventure lands, our sanctuaries, our access to open space. One big reason we love and live in mountain towns has nothing to do with the town its self. While walking from one end of town to the other in less than ten minutes and knowing more than 50% of the people standing in line with you at the local coffee shop has its perks, it’s the potential that lies beyond the city limits, at the end of winding dirt roads, along singletrack trails, atop snowy mountain peaks, and along quiet mountain streams that draws a lot of us mountain-dwellers to this life.
However, the elements that bring us here are also put at risk as more and more people enjoy the great outdoors. Much of the “performance gear” – the soft-shell jackets, technical packs, baselayers, and weather protection – require a huge amount of energy and non-renewable environmental resources to create. Not to mention, the transportation of gear (and people) to these places comes at the cost of a high carbon footprint. All of the above impact the climate, open spaces and ecosystems around us.
But we’re not about to stay home – the outdoor community is not one to sit back in helplessness. Nope, instead we’re focusing on creative ways to reduce our environmental footprint while increasing our trail time. We, as individuals and companies who respect these big backyards, are finding ways to reduce our resource consumption and source necessary resources consciously and sustainably.
Voormi, a craft apparel brand based in Pagosa Springs, Colorado, is giving us a powerful lesson in how to make the best of our backcountry environments, while preserving natural resources and acting as stewards of these mighty lands.
Built around the remote and rugged lifestyle of the Southern San Juan Mountains, Voormi makes performance gear using micron merino fabrics. In a place surrounded by over 1.8 million acres of National Forest, Voormi has chosen to source all of their wool from the local regions of the high Rocky Mountains. From sheep to fabric to jacket, Voormi is creating a truly local and sustainable product that’s built to last a long time (we’re not in a buy new gear every year environment anymore), support local craftspeople, create a symbiotic relationship between people and local landscapes, and create a product that arrives at your doorstep without the need for thousands of gallons of oil and gas to get there.
“To us, being local is about being connected. It’s about being nimble. And most of all it’s about being able to build with a true dedication to purpose,” they explain.
We sat down with Timm Smith of the Voormi team to learn more about why and how this crew is dedicating themselves to changing the way we play and work outdoors.
Sarah Betts: So what’s the Voormi story? Why did you decide to source local wool and create a company dedicated to doing business in the outdoor industry differently?
Timm Smith: When we first started the company, we did so with a passion for making a significant change not only what we wear, but how it gets to us. At the time, in early 2010, a significant wave of supply chain consolidation and off-shoring had led to what we believed was a ‘sea of sameness’ in the industry. Our goal in starting the company was to hit the reset button, focusing first on innovation in natural fibers, and then on building an extremely agile local supply chain for rapid iteration and development.
We started by drawing a box around the United States, tapping in to everyone from The American Sheep Industry to a dispersed network of Textile Mills and factories around the country. As we grew, it became our goal to drive a continuously more local supply chain at each progressive horizon of the business (a concept we call ‘Growing up – Growing in’). Soon, we had the infrastructure to start supporting and growing small cut and sew operations across the state (including the expansion of our operation here in Pagosa Springs). This approach not only allows for faster innovation cycles, but also allows us to begin to make a significant economic impact in rural areas, which is now one of our guiding principles for the brand.
SB: How much of your wool is sourced from sheep raised in the Colorado mountains? How many sheep does it take to support your production right now?
TS: While a lot of our wool does come from Colorado, we actually draw our boundaries a little more broadly around the Rocky Mountain Region, including a region that spans roughly from northern New Mexico to Montana. Rather than focus on one ranch, we set out each spring in search of the best seasonal clip. The unifying factor is the ‘crimpy’ spring-like properties of wool grown in high-elevation climates. In terms of numbers, it varies season to season. It takes about one pound of clean wool to make a garment, which is about two pounds of ‘greasy’ wool (straight from the sheep’s back). A Rambouillet (the variety of sheep we source from) sheep’s fleece is about ten to fifteen pounds, so you’re looking at about five to seven garments per sheep.
SB: What’s unique about the breed of sheep you source from and why does this make your merino fabrics different?
TS: We source our wool primarily from Rambouillet sheep raised in the high elevation regions of the Rockies. The unique combination of breed and environment facilitates the growth of a very unique spring-like crimpy fiber. This not only makes the fiber stronger and more resilient – springy things can absorb a lot of energy before they break – but also means that the fibers don’t pack as tightly when spun in to yarn. This ‘low density packing’ leads to better thermal performance
SB: What is involved in making your merino – from sheep to cloth what does it take?
TS: Sheep are typically sheared in the spring after a winter of building their fleece. That wool is then sold at auction, and sent to a facility on the east coast for cleaning. At the cleaning facility, all of the dirt and grease is washed out, and about 50% of that wool comes out as clean white wool. That wool is then combed multiple times (to remove short fibers), dyed, and spun in to yarn. We control every detail in the yarn to drive the right balance of strength and softness. That yarn is then sent to a weaving facility where it is turned in to fabric through our engineered knitting/weaving processes. That fabric is then sent to the cut and sew factory where it is turned in to garments
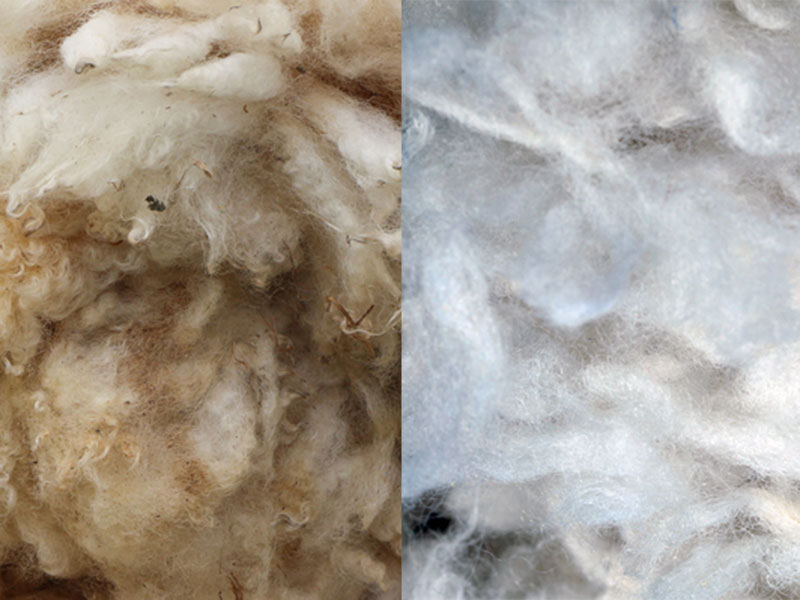
SB: What else do you take into consideration when making the material? What dyes do you use, how does the merino functionality add to the products you are making?
TS: Our Precision Knitting & Weaving platforms are a key point of differentiation for us. While most companies rely on large global suppliers to develop their textiles, we design and develop each and every one of our textiles from scratch, right here in the US. From our award winning nylon re-enforced SURFACE HARDENED(TM) Thermal Wool, to our genre blurring CORE CONSTRUCTION(tm) Fabric, this tight control over R&D has led to some pretty unique textiles over the years. It is continuously our goal to push the performance of natural fibers through these advanced construction methods.
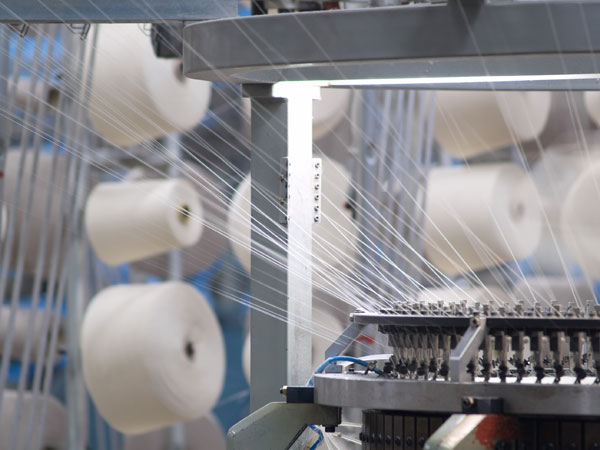
SB: How does sourcing materials locally impact the business in terms of sales, quality, and price?
TS: Setting up a local supply chain from scratch is not the ‘easy way’ to start a business. We certainly have our bruises, but what we can say now is that our ‘local approach’ to sourcing has become a significant competitive advantage for us. Not only are we faster to market, our ability to innovate is hands down better than if we had gone the traditional ‘big industry/global’ sourcing route. Additionally, we believe that the accountability of local sourcing drives better product. There’s nothing more honest than sitting in a bar next to a guy who bought the clothing you personally put your hands on.
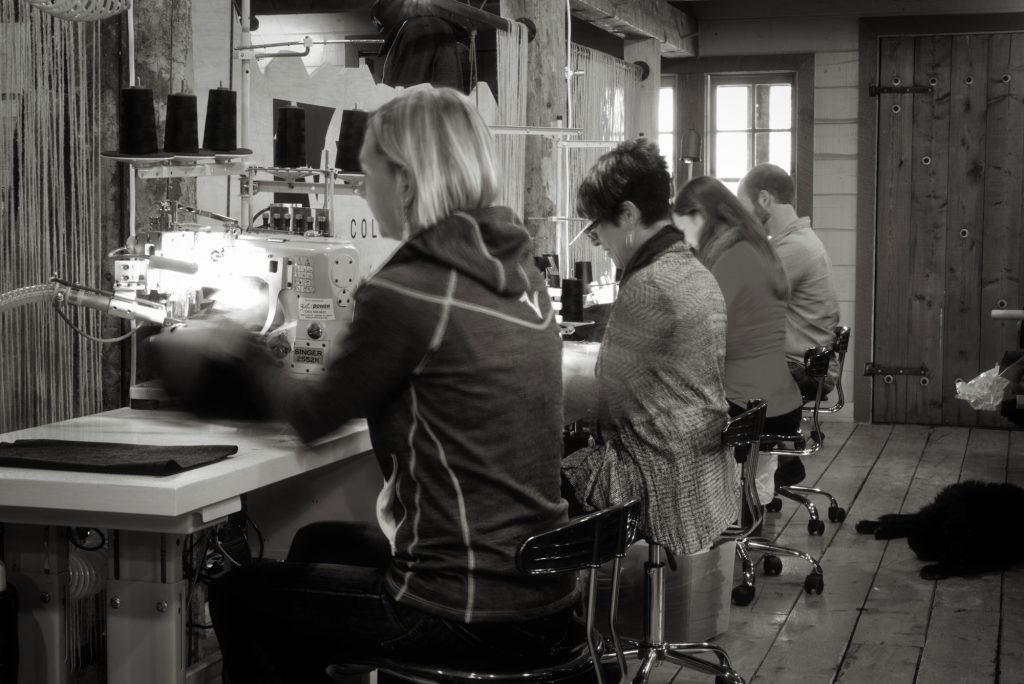
SB: Why does Voormi use wool rather than other products?
TS: Honestly, if you look at the long history of alpinist clothing, it is not until very recently that the world of man-made fibers has even been a part of the discussion. The unique thermal/moisture managing and anti-microbial properties of wool have made it a ‘go to’ fiber for a very long time. To this day, it is impossible to emulate the unique natural properties of wool in an extruded man-made fiber. That said, there are some things about wool that we felt could be better (abrasion resistance, wicking properties, etc.). Our vision was to leverage cutting edge knitting and weaving techniques to ‘supercharge wool’ and remove its Achilles heels. It was our belief that introducing ‘just enough’ synthetic fiber in ‘just the right places’ without destroying the natural wonder-properties of wool was the next big breakthrough for outdoor clothing!